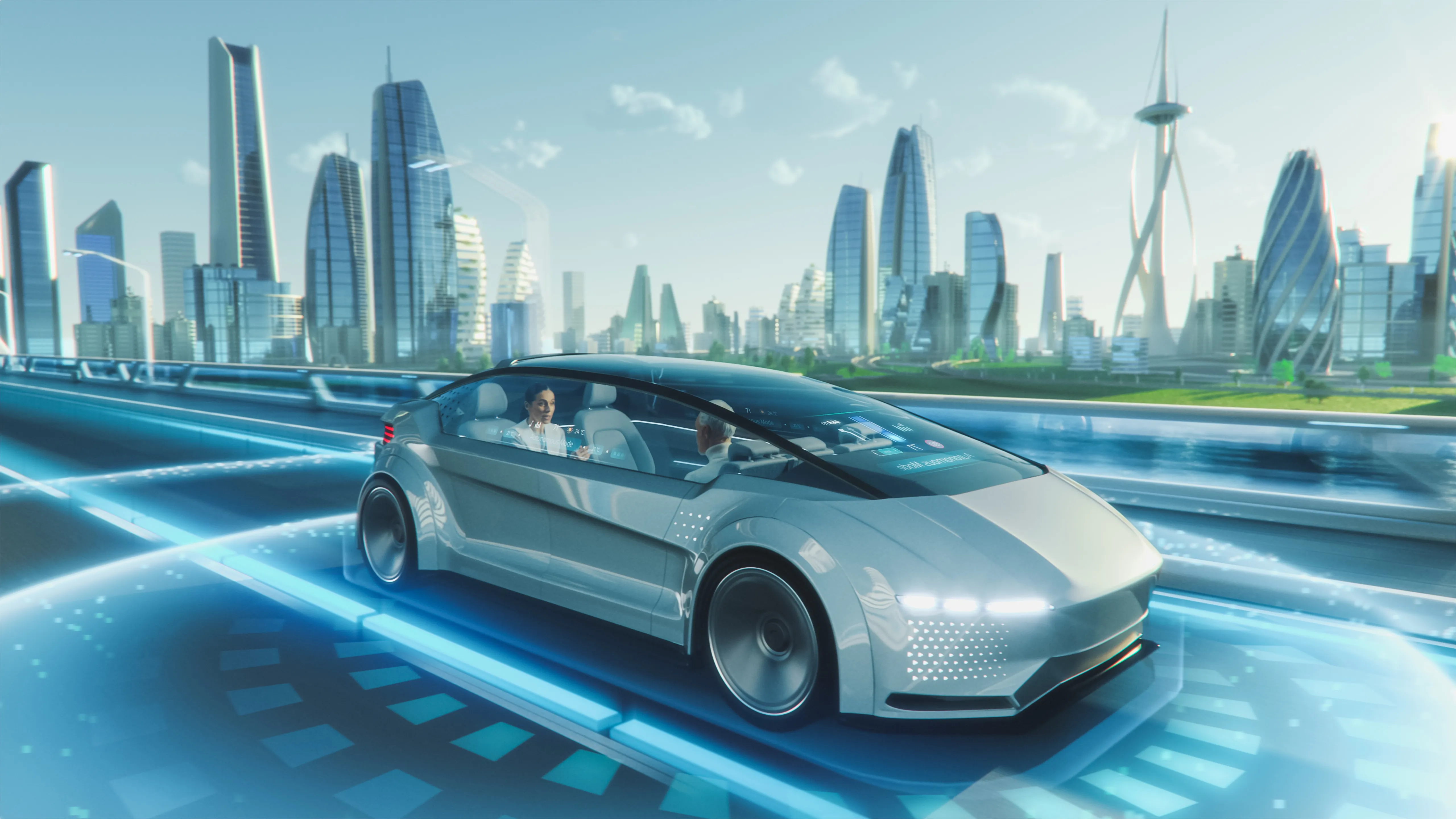
Plastics Technologies Driving Next Evolution of NEVs
China's Ministry of Industry and Information Technology announced the mandatory national standard titled “Energy Consumption Limits for Electric Vehicles - Part 1: Passenger Cars” (Draft for Comments) on August 21, 2024. This standard establishes electric consumption limits for new energy vehicles (NEVs) as a mandatory requirement for the first time. The energy consumption of NEVs is closely linked to vehicle lightweighting, and a key advantage of high-performance plastics is their potential to replace heavier materials.
Meanwhile, autonomous driving technology is emerging as the “brain” of NEVs. The unique properties of high-performance plastics can meet the stringent requirements of related applications. Consequently, the use of automotive plastics in vehicle manufacturing is steadily increasing, and their applications are becoming more diverse in the automotive industry.
Source: Song Yuan, Lecturer, Shanghai Donghai Vocational & Technical College; Adsale Plastics Network(www.AdsaleCPRJ.com)
The calling for comments of the mandatory nation standard indicates the government's intention to enhance the energy consumption thresholds for vehicle models and to refine the management mechanisms governing the energy consumption of NEVs. These measures aim to promote the healthy development of the industry and encourage technological progress.
For models with fewer than three rows of seats and without four-wheel drive, energy consumption limits range from 10.1 kWh to 19.1 kWh per 100 km. Specifically, models with a curb weight between 1.09 tons and 2.71 tons must maintain their electric consumption below 13.92 kWh per 100 km. However, industry statistics indicate that as of August this year, only about 60% of these models meet the standard. This highlights the urgent need for effective means to reduce electric consumption.
The national standard requirement clearly indicates that curb weight will be a key assessment criterion. The high curb weight of NEVs is closely linked to their powertrains. For instance, many battery packs from various brands weigh over 500 kg, with some even exceeding 700 kg.
Currently, this mandatory national standard is in the consultation stage. Based on industry practices, it may take about two years before the official release. Therefore, this is the ideal window for automakers to refine their lightweight technology strategies.
The traditional fuel vehicle powertrain (engine and transmission) operates in a high-heat, high-wear environment, resulting in limited use of plastic parts. In contrast, the new energy power system, particularly the battery pack management system and other components, offers more favorable working conditions, making it easier to incorporate automotive plastics.
(1) Need for flame retardant
Automotive plastics play a crucial role in the thermal management of battery packs. Thermoplastics with excellent flame retardant property can mitigate the risk of overheating in high-temperature and pressurized environments. Notably, polypropylene compounds (PPc) and long glass fiber (LGF) reinforced PP stand out.
Leveraging the strengths of thermoplastics, SABIC has developed an innovative battery pack concept that integrates individual batteries into pouch cells. These cells are placed within a thin-walled housing molded with 30% glass fiber filled, flame-retardant PPc.
LG Chem and LX Hausys have also collaboratively created a special flame-retardant continuous fiber thermoplastic (CFT) designed to delay battery thermal runaway.
(2) Need for dust and water resistance
Power battery packs require stringent dustproof and waterproof ratings, with the industry standard being IP67. Some automakers, such as Geely, NETA, and ARCFOX, even claim capabilities of reaching IP68.
The key to enhancing the IP performance of battery packs lies in the sealing and securing of components around electrical connectors. These connectors, critical for maintaining the interface between the interior and exterior of the battery pack, must endure mechanical stress and environmental fluctuation.
Utilizing high-strength, wear-resistant materials like polyamide (PA) or polycarbonate (PC) can ensure the stability and sealing of connections, preventing moisture, dust, and other impurities from entering the inner part, thereby guaranteeing the reliable operation of the electrical system.
In addition, the significant gas generated by the battery pack after thermal runaway must be discharged promptly to prevent potential explosion. The support structure for safety devices, such as explosion-proof valves, is often made of specially designed plastic materials that can react quickly in emergencies. This ensures effective internal pressure release, further enhancing the safety of the battery pack.
The structural components of battery pack are vital parts of the electric vehicle energy system, significantly influencing the vehicle's overall performance, safety, and driving range.
Traditionally, high-strength steel has been the material of choice for the stamping forming structure of battery packs, owing to its excellent mechanical strength and impact resistance, which helps maintain structural integrity under complex working conditions.
In recent years, there has been a growing trend toward the use of automotive plastics in battery pack design, particularly in module housings and pack sealing covers. This shift aims to enhance lightweighting while still ensuring performance and safety.
Plastic materials such as PC, PA (particularly reinforced), and polyurethane (PU) not only possess densities much lower than steel, but also achieve comparable or even superior mechanical property and environmental aging resistance under specific formulations and processes.
For instance, the LGF reinforced flame-retardant PA material newly introduced by Shanghai PRET Composites Co., Ltd. is used to replace steel in structural components of battery packs. The material reduces component weight by 40% and lowers manufacturing costs by 15%.
Structural components of battery packs face challenges from mechanical vibration, high temperatures, high humidity, ultraviolet radiation, and chemical corrosion due to their harsh working environment. This imposes stringent performance requirements on materials.
To satisfy these requirements, the industry has made substantial advancements through ongoing exploration and innovation. A notable example is the successful application of PU solutions for battery pack top covers.
In a series of rigorous standardized tests, including assessments of mechanical properties, high-temperature and high-humidity aging, xenon lamp aging, acid and alkali resistance, high-temperature resistance, and insulation properties, PU materials have proven their viability and superiority as structural materials for battery packs.
The Baydur® HP-RTM (High-Pressure Resin Transfer Molding) top cover for battery packs developed by Covestro is a key application of PU in NEVs. It is flame-retardant, lightweight and can be as thin as 0.8 mm.
The “Opinions of the General Office of the CPC Central Committee and the General Office of the State Council on Accelerating the Construction of a Unified and Open Transportation Market”, was released in December 2024, emphasizes the continuation of pilot applications, including autonomous driving, to promote the green and intelligent transformation of transportation.
Over 50 cities in China have implemented autonomous driving demonstration policies, with automakers highlighting autonomous driving features as key selling points for NEVs.
Autonomous driving technology is emerging as a new productive force supporting the development of NEVs. It not only fosters new business models, such as shared autonomous taxi services, but also drives innovation in related technologies.
The Advanced Driver Assistance System (ADAS) employs sensors to detect and collect data, integrating it with navigation information for comprehensive analysis. Among its functions, the Navigate on Autopilot (NOA) stands out.
NOA is a technology that combines assisted driving with navigation capabilities. When a vehicle is on a highway, NOA enables it to automatically change lanes, enter and exit ramps, adjust speed, as well as manage lights based on the onboard navigation route.
ADAS has specific and unique material requirements, and plastics offer significant potential for related applications. For instance, millimeter-wave radar delivers reliable and high-resolution information for long-range target, while the radar fairing protects the internal high-frequency antenna from weather and environmental damage. The materials used for the fairing must possess high strength and ensure that penetrating radio waves remain unaffected.
High-performance engineering plastics are not only easy to process but also exhibit excellent heat and chemical resistance. Additionally, certain plastics have a lower dielectric constant (Dk), enabling the radar's emitted radio waves to penetrate effectively, thus meeting the material requirements for millimeter-wave radar fairings.
As the ADAS market continues to expand, material suppliers are developing cutting-edge solutions. For instance, Envalior has recently launched a laser-weldable thermoplastic product portfolio for automotive radar, which includes polybutylene terephthalate (PBT), polyphenylene sulfide (PPS), and PBT + PC grades.
SABIC has introduced two new modified materials with a high dissipation factor (Df), enabling efficient noise absorption. This improvement enhances the signal-to-noise ratio of millimeter-wave absorbing devices, leading to increased sensor accuracy and transmission range. The ultra-high flow and minimal warpage properties offer greater design flexibility.
Advances in materials science and innovations in manufacturing process show a promising future for the application of automotive plastics in the power systems of NEVs. The choice of materials for battery pack structural components will become increasingly diversified. Striking a balance between lightweight design and high performance will emerge as a key focus for the industry moving forward. Furthermore, automotive plastics can enhance the efficiency and safety of autonomous driving, facilitating the development of intelligent vehicles and transforming the transportation landscape.