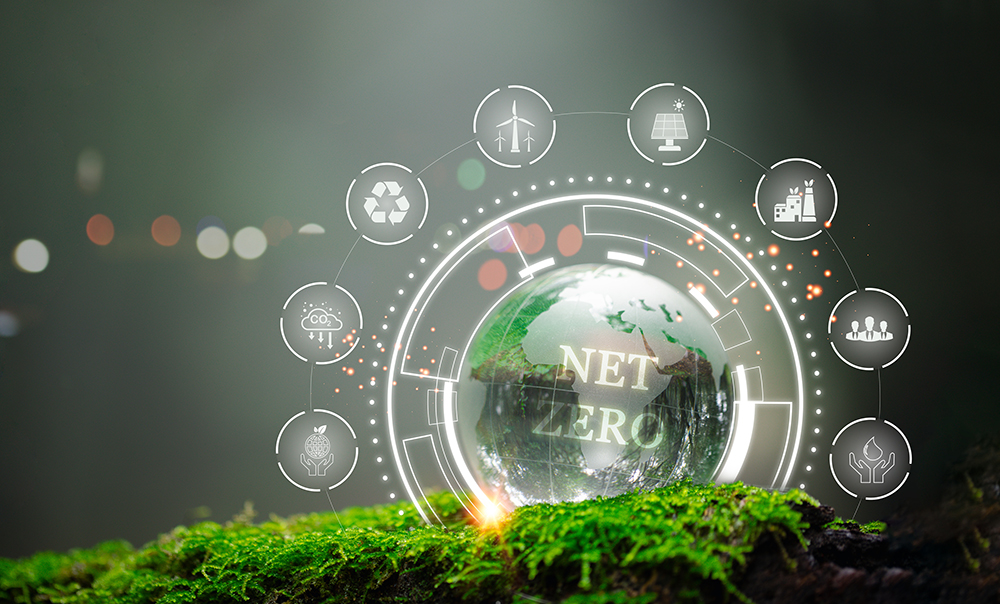
The global plastics recycling market size is forecast to grow at a 7.71% CAGR from 2024 and reach US$77.89 billion by 2031
(Source: iStock)
Plastics Transformation Turns the Page in Circular Economy
The imminent conclusion of the legally binding Global Plastics Treaty in 2024 and the joint release of the Sunnylands Statement by China and the United States send a strong signal to the world for global collaboration in actively addressing plastic pollution. This brings unprecedented development opportunities for the plastics recycling industry.
According to the latest research report from InsightAce Analytics, the global plastics recycling market size is forecast to grow at a 7.71% CAGR from 2024 and reach US$77.89 billion by 2031. Faced with this immense opportunity, end-user brands, plastic product manufacturing companies, recycled plastics and recycling companies are seizing the chance for business growth, while also fulfilling their social responsibilities.
Source: Adsale Plastics Network (www.AdsaleCPRJ.com)
Compared to mechanical recycling, which has already established an industrial scale, chemical recycling is still an emerging technology. However, in recent years, we have seen European chemical companies continuously investing in chemical recycling, and more Chinese companies are actively participating in the chemical recycling boom. In addition, new recycling technologies, such as biological recycling, have also begun to operate on a larger scale, further enriching the means of plastic waste processing.
Thanks to its superior plastic waste processing and crude oil substitution capabilities, chemical recycling has been driven by significant investment from leading international petrochemical and processing companies. For example, Saudi Basic Industries Corporation (SABIC) has partnered with Plastic Energy, the UK-based chemical recycling company, to advance the processing of mixed post-consumer plastics; ExxonMobil and Sealed Air (SEE) use chemical recycling technology to convert plastic waste into new food-grade packaging; Coperion is supplying a complete system of the chemical recycling of polymethyl methacrylate (PMMA) to a plastic product manufacturer in Dubai.
In addition to the recycling of fossil-based plastics, there have been new developments in the recycling of bio-based plastics such as polylactic acid (PLA). TotalEnergies Corbion utilizes depolymerization technology to produce Luminy® rPLA, which has up to 30% recycled content, offering performance comparable to virgin PLA.
Notably, China has been developing rapidly in the field of chemical recycling in recent years. For example, Tianjin Bohai Chemical, China Tianying and Jiutai New Material have successively collaborated with international companies like Honeywell to launch chemical recycling projects. Such Sino-foreign collaboration further advances the development of chemical recycling in China. In 2023, Zhejiang Jiaren New Materials made the global debut of its recycled dimethyl terephthalate (DMT), filling the gap in China's recycled DMT sector. Many other Chinese companies, including Sinopec, CR Chemical Materials, , CR Chemical Materials, Wanhua Chemical and Beijing Aerospace Petrochemical are also actively implementing chemical recycling projects.
In addition to mechanical and chemical recycling, biological recycling is also emerging as a new plastics recycling method. In 2023, the biological recycling technology for polyethylene terephthalate (PET) was selected by the International Union of Pure and Applied Chemistry (IUPAC) as one of the “Top Ten Emerging Technologies of the Year". The French company Carbios has been granted the license to build and operate the world's first PET biological recycling plant. International giants such as Coca Cola and Procter & Gamble (P&G) have also successfully applied PET biological recycling technology in production and are promoting the products globally.
As one of the main sources of plastic waste, post-consumer plastic packaging waste has always been the focus of global plastics recycling and circular economy. As the pioneer in the circular economy for plastics, Europe has made enormous efforts in this area. Germany, France and the UK have enacted regulations for plastic packaging to accelerate the implementation of packaging waste management. In 2023, the European Union further proposed the Packaging and Packaging Waste Regulation (PPWR), which sets out new rules for the proportion of recycled plastic in packaging.
Meanwhile, international brands such as Coca-Cola, PepsiCo, P&G, and Unilever have been actively fulfilling their social responsibilities by setting targets for the use of recycled plastic in packaging at different time intervals (by 2025/2030), thus encouraging the participation from more stakeholders in plastic packaging circularity worldwide.
In particular, with the development of bottle-to-bottle recycling solutions and the expansion of food-contact recycled plastics, the PET bottle recycling industry is moving towards efficient and intelligent processing. For example, Starlinger, an Austrian supplier of plastics recycling machinery, has developed the recoSTAR PET system for bottle-to-bottle recycling, which saves 25% of energy consumption, increases production by 15%, and helps reduce production costs by approximately 21%.
Flexible packaging has long been identified as a challenge in plastics recycling. In recent years, leading global food brands, packaging suppliers, and recycling technology providers have joined forces to promote the circular use of flexible packaging. Mondelēz International and Amcor have built Australia's first chemical recycling facilities, processing 20,000 tons of plastic waste annually, with Mondelēz International reapplying recycled materials to product packaging. Nestlé has invested £7 million in Impact Recycling, a UK recycling technology supplier, to establish a new plant that converts hard-to-recycle flexible packaging into plastic pellets for reuse in flexible packaging production.
As the global automotive supply chain increasingly demands carbon reduction, the technology for producing recycled plastics continues to improve and innovate, unlocking the huge growth potential of the global automotive recycled plastics market.
Many global automotive giants, such as Volvo, BMW, Mercedes Benz, Ford, etc., have set goals for the use of recyclable/renewable plastics. For example, starting from 2025, Volvo aims to have at least 25% of the plastics in their vehicles come from recycled materials, and Ford aims to use 20% recycled and renewable plastics in new car designs in their North American and European factories. BMW aims to have 40% of the plastics in their cars made from recyclable thermoplastics by 2030, and Mercedes-Benz is set to increase the proportion of secondary raw materials used in their vehicles to 40%.
In July 2023, the European Commission proposed new regulations on End-of-life vehicles (ELVs). The proposal states that new vehicles should contain at least 25% recycled plastics, with a quarter of that coming from End-of-life vehicles. This initiative will further encourage automotive companies to adopt recycled plastics, especially in vehicles exported to the European market.
In fact, many automotive plastic suppliers have begun actively exploring and implementing the use of recycled plastics with automakers and automotive component manufacturers. Eastman has partnered with global automotive interior supplier Yanfeng to recycle plastics from ELVs and produce polyester and cellulose thermoplastics. Toray Industries has successfully recovered glass fiber reinforced nylon 6 from ELVs with chemical recycling technology and reapplied the recycled materials in new Honda vehicles. Chinese companies Shanghai Pret Composites Co. and VARY New Material have teamed up to develop high-quality post-consumer recycled (PCR) materials for automotive applications.
In addition to the automotive industry, the use of recycled materials in home appliances and consumer electronics is also on the rise. According to a report by Grand View Research, the recycled plastics market for global consumer electronics is expected to reach US$139 million by 2023 and continues to grow at a CAGR of 10.8% from 2024 to 2033.
Global consumer electronics brands, such as Microsoft, Lenovo, Huawei, and home appliances brand Panasonic are actively promoting the circular economy and the recycling of their products. Panasonic and Jiangxi Green Recycling advanced the development of PCR resins in 2023 to develop high-quality industrial products such as home appliances; Microsoft collaborated with SABIC to launch the first series of Surface devices and power supply casings made from ocean bound plastics (OBP).
Huawei’s HUAWEI Watch 4 smartwatch uses the industry’s first recycled nylon composite strap; Lenovo adopts recycled carbon fiber as a reinforcing filler in the ThinkPad X1 Carbon Gen 12.
Apart from materials, processing technology is also constantly upgrading. In order to enhance the efficiency of recycled plastic production, GENIUS, a German recycling equipment supplier, has developed a strand pelletizing system for complex materials in electronic and electrical equipment, enabling quick pelletizing of recycled ABS and PS materials.
The application of recycled polyester fibers in the fashion and textile industry is rapidly growing. According to statistics from Textile Exchange, the use of recycled polyester fibers in the global fashion and textile market is expected to increase from 14% in 2019 to 45% in 2025. Global fashion brands such as Adidas, UNIQLO and H&M have announced sustainable development commitments for 2024/2025/2030, targeting to use 30% to 100% recycled materials in their products.
In the sports and apparel sector, Puma is expanding the use of its Re:Fibre polyester recycling technology; starting from 2024, most of the company's replica jerseys for soccer clubs will be made from fibers recycled from old clothes. UNIQLO launched the "Doraemon Sustainability Mode" product series for spring and summer of 2023, which is made entirely from 100% recycled fabrics.
Furthermore, food delivery and FMCG enterprises are also exploring plastics recycling across the value chain. Meituan’s Green Tech Fund and Donghua University co-developed the first low-carbon polypropylene fabric made from recycled takeaway container materials, which will be used to make quick-drying T-shirts. Additionally, Meituan also joined hands with M&G Stationery to launch the carbon-neutral stationery series using recycled plastics from food containers.
With the recycled polypropylene pellets from takeaway containers, Ele.me, the online food delivery platform, and TRASHAUS, an integrated innovation company for circular economy, utilized recycled PP pellets from takeaway food containers to 3D print various peripheral products, such as recycled phone holders, storage boxes, and PP pencil holders.
To conclude, more and more end-user brands, whether in the packaging, automotive, home appliances and consumer electronics, fashion and textile and fashion, or food takeaway sectors, are starting to work closely with upstream and downstream players in the plastics recycling supply chain.
The high-potential plastics recycling market is an arena attracting more players to join hands to accelerate the development of circular economy for plastics.