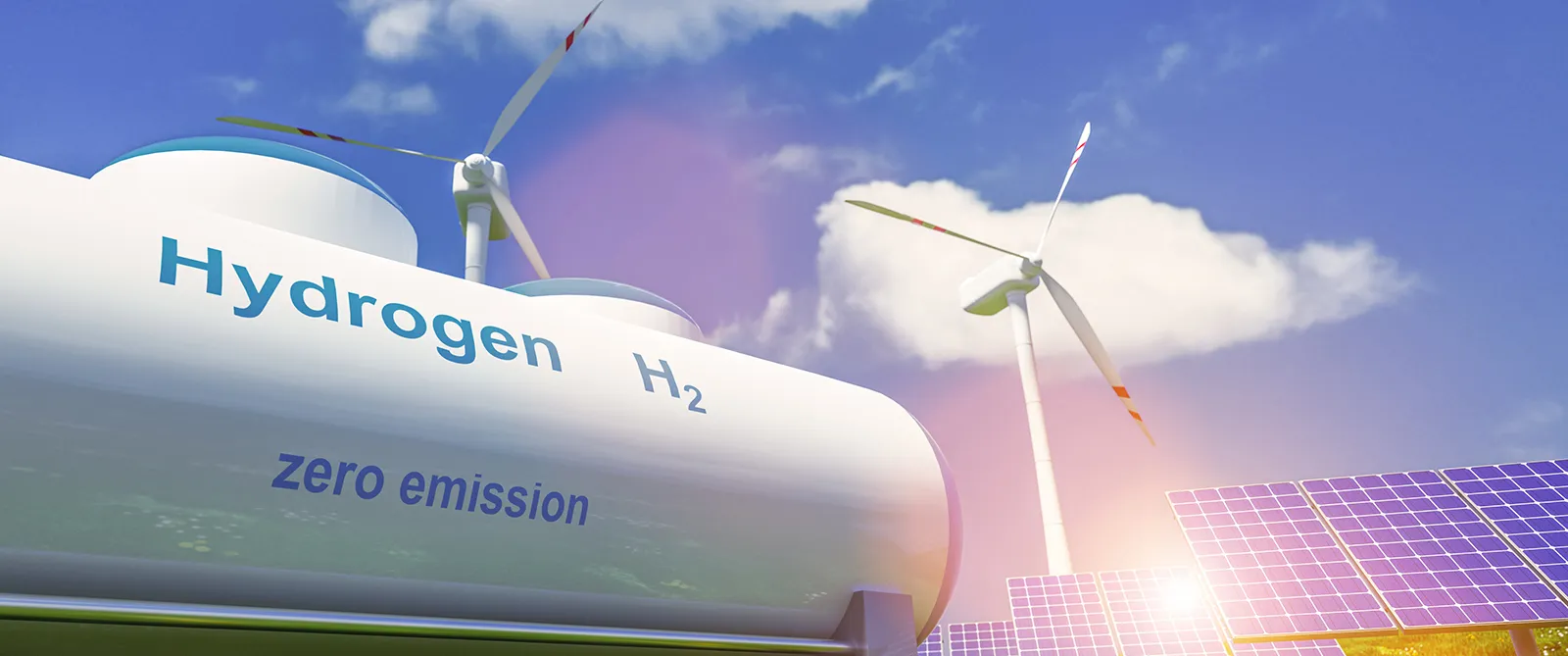
Innovative Materials Empower the New Energy Industry
The new energy industry is experiencing a remarkable growth, and the plastics and rubber industries are playing a crucial role in its success.
To begin with, plastics and rubber materials are widely used in the manufacturing of tape seals for solar panels and hydraulic sealing pads for wind power generation equipment. These products not only offer excellent sealing performance but also exhibit high temperature resistance, corrosion resistance, and weather resistance. As a result, they can withstand harsh outdoor conditions and effectively safeguard the normal operation of equipment.
Furthermore, plastics and rubber pipes and hoses find extensive applications in solar water heaters, biomass energy, and biofuels. These products provide reliable load-bearing capacity and protection, facilitating the smooth transportation of energy resources.
From the viewpoints of production, transportation, and storage, the plastics and rubber industries serve as a solid foundation for the sustainable development of the new energy sector. With the growing demand for clean energy, this industry will continue to focus on innovation and development, making significant contributions to the overall growth and prosperity of the new energy industry.
New Energy Related Products
New Energy Related Videos
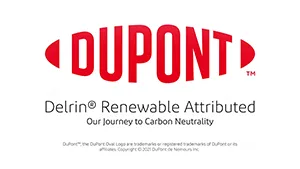
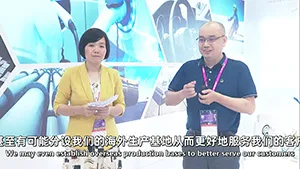
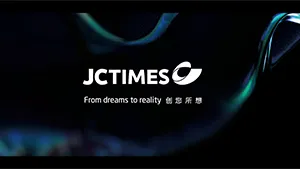
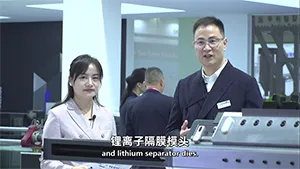
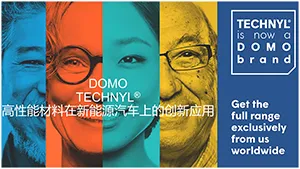
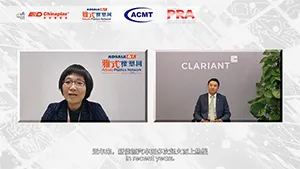
Industry News

RADICI PLASTICS (SUZHOU) CO., LTD.
As the global leader polyamide material supplier, RADICI has multiple solution for the Electrification, intelligentize, safety and environmental friendly which widely use for the NEV, EE and industrial application. At present, RADICI can provide the full solution of the flame retardant polyamide material with full UL card certification. RADICI has been using material recovered from end-of-life products for over 15 years, and thus can provide the fully recycled grade-HERAMID and partial recycled grade-RADILON(also for prime grade) with Environmental product Declaration(EPD) certification, which also have got many end user approval including BMW/FORD/FCA/BOSCH/GM/Volvo.
BORCH MACHINERY CO., LTD.
Borche’s new generation electric machine BD series is featured with direct drive technology. It is an achievement of Borche 20 years’ research and development on electric injection molding machine. BD series integrates the advantages of independent intellectual property rights, direct-drive structure, smart control of injection molding, process optimization by big data. It is widely applied in many industries such as medical health, new energy vehicles, intelligent home appliances, 3C products, etc.
STAR-BETTER (SHANGHAI) CHEMICAL MATERIALS CO., LTD.
With the upgrading of household appliances, automobiles, E&E and other industries, the application of new materials, new technologies and new energy has become an urgent need, and it also greatly promotes the development of flame retardant polymer materials. Therefore, with the enhancement of people's awareness of environmental safety, halogen-free flame retardant instead of halogen-free flame retardant has become the development trend of flame retardant materials. EPFR-100DP is an environmentally friendly polyolefin flame retardant with phosphorus and nitrogen as flame retardant elements. Designed for a variety of flame retardant polypropylene products, it can also be used for other polyolefin flame retardant products. EPFR-100DP contains acid source, air source and carbon source, and plays a flame retardant role by the mechanism of carbon formation and expansion. PP with EPFR-100DP flame retardant which reached UL 94 V-0 (1.6mm), passed the 70℃168 hours immersion test (UL746C), and the GWIT 750℃ and GWFI 960℃ hot wire test.
POLYPLASTICS (SHANGHAI) LTD.
This cellulose is a renewable, inedible biomaterial that is at no risk of ever running out. Also, by incorporating this cellulose into resin as a reinforcing material, the CO2 emissions over the entire life cycle of the product can be reduced. It further contributes to reduced CO2 emissions thanks to the greater fuel efficiency achieved when it is used to lighten the parts of vehicles.Advantages of long cellulose fiber reinforced thermoplastics
• Able to reduce CO2 emissions over the entire product life cycle.
• Contributes to reduced usage of petroleum-based materials.
• Because cellulose fibre of stable quality is used, there is less likelihood of gas production during the fabrication process compared with natural fibre reinforced resins, resulting in products of a stable quality.

GUANGDONG BLESSON PRECISION MACHINERY CO., LTD
The features of our Lithium-Ion Battery Separator Film High-Speed Winding Unit include:1. Precise double tension control system.
The ultra-light carbon fiber roller designed and manufactured with the latest advanced technology has super dynamic response ability, which can control and adjust the production tension and winding tension of the film separately.
2. Integrated anti vibration system.
Special steel with over aging treatment is adopted to make the winder run at high speed and stably with very low noise through precise processing and high standard assembly requirements.
3. No adhesive or tape is required for film roll changeover.
The electrostatic roll changing mode is adopted, and the winding tension is kept stable through the whole roll changing process, so that the outer film roll also has good winding quality, and there will be no film waste or unnecessary adhesives.

ZHEJIANG JINGCHENG MOLD MACHINERY CO., LTD
The structural design of lithium battery die series from JINGCHENG is innovative and unique. Through the multiplication technology of the multi-layer distributor and the composite technology in the three-layer membrane, the mechanical performance and barrier performance of the diaphragm can be effectively improved, and the heat resistance and cold resistance of the diaphragm can be significantly improved. Besides, the thickness uniformity of the diaphragm is good, and the deviation is small. High automation and high-speed production can be achieved through two-way stretching.With automatic fine adjustment structure, the mold lip can be adjusted quickly and accurately to effectively control the product accuracy. Through the special process of laser hardening+electroplating, the sharp corner of the shaping section of the three-layer co-extrusion die head can make the sharp corner of the die lip reach R0.01mm, avoid the line phenomenon formed at the outlet during the production process, and improve the quality of the diaphragm.

GUANGDONG JISHUO NEW MATERIALS CO. , LTD.
As a power module, Lithium batteries charge & discharge frequently and release great amount of heat, which may cause safety issues. In developed countries, people use low smoke flame-retardant materials to prevent conflagrations and personal injuries. This has been practiced for years and it is proved to be one of the effective safety protection measures.JiShuos flame-retardant polypropylene (PP-JS2017) is mainly used in Lithium battery modules for rail transit system (high-speed railway) and new energy vehicles. It is halogen free, low smoke, thin wall, easy to shape and very smooth on surface. It is EN45545-2 (flame retardancy of rail vehicle materials) certified. Colors and functions can be customized as per requests.