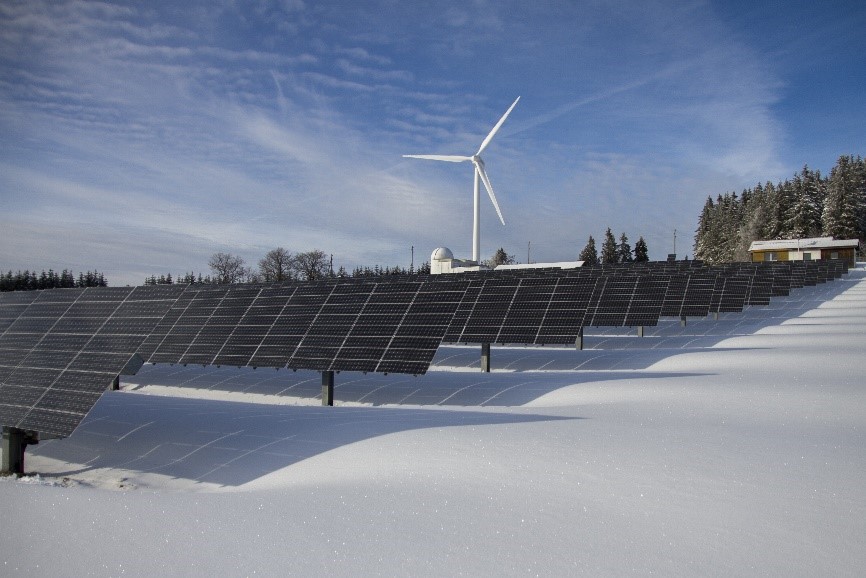
The renewable energy market is estimated to grow at a CAGR of 8.91% between 2022 and 2027, according to Technavio.
(Source: Pixabay)
Plastics, the Game-Changer for New Energy Transformation
New energy refers to renewable energy sources other than fossil fuels, such as solar, wind, hydrogen, water, etc. They are not only abundant and inexhaustible, but also produces less carbon emissions and provides enormous benefits for our environment. The wider application of the clean energy sources has been made possible by energy storage.
The global renewable energy market is estimated to grow at a CAGR of 8.91% between 2022 and 2027, according to Technavio, of which 73% will be contributed by the significantly growing Asia-Pacific market. Remarkably, continuous innovation in plastics empowers the burgeoning development of the new energy industry with new lightweight, high-performance, low-cost and low-carbon materials. By leveraging the unique properties of plastics, more sophisticated designs, optimized components and efficient processing technologies are emerging.
Source: Adsale Plastics Network(www.AdsaleCPRJ.com)
Global renewable energy capacity was projected to soar by 107 gigawatts (GW), the largest absolute increase ever, to more than 440 GW in 2023, according to the market update by International Energy Agency (IEA), an intergovernmental organization. Among them, photovoltaic (PV) capacity accounts for two-thirds of the increase.
Plastic is increasingly used to produce modern solar panel parts, such as encapsulant films, backsheet, frontsheet, structural parts and other components, playing an essential role in the development of PV system.
Replacing glass and aluminum, plastic has a list of advantages including being lightweight, low-cost and efficient for manufacturing, and high-performance. It also provides protection from moisture, temperature and UV light.
As plastic is lighter than glass and aluminum, solar panels made with plastic can be installed on a larger number of roofs. Various solar panel manufactures have developed lightweight products with environmental considerations, enhancing its sustainable benefits.
Solarge, a manufacturer of solar panels, has partnered with SABIC to develop lightweight low-carbon solar panel. SABIC’s differentiated polypropylene (PP) compounds for solar panel offer more than 50% weight reduction and 25% carbon footprint reduction.
Another manufacturer – Merlin Solar, leverages the lightweight property of its stronger structured solar panel, which weighs considerably less than a standard product because it uses plastic instead of glass front shield, to market its product.
South Korean company LG Chem has developed LUPOY EU5201, an engineering plastic composed of acrylonitrile styrene acrylate (ASA) with polycarbonate (PC) as a base and reinforced with glass fibers. The strong and lightweight material is used to replace aluminum for the production of solar panel frame. Besides, it can also be produced with post-consumer recycled (PCR) PC.
Manufacturing of solar panels made with plastic also requires less time and cost without compromising functionality and durability. Borouge’s Quentys Encapsulant Films and PP compounds for backsheet feature superior resistance to UV light, high water barrier and a lamination that does not require chemical reaction.
Borouge also offers food-grade high density polyethylene (HDPE) material for floating photovoltaic (FPV) systems. The Environmental Stress-Crack Resistance (ESCR) HDPE features outstanding mechanical properties with increased durability, as well as recyclability.
While wind power offers advantages as a renewable energy source, the wind energy sector faces the challenge of high manufacturing costs. Wind turbine blades, which account for 20%-25% of overall turbine costs, play a crucial role in making wind energy more competitive and accessible. The key lies in developing lightweight blades with optimized designs.
Advanced polymer materials, known for their lightweight nature and enhanced performance, present exciting opportunities for the design of new wind turbine blades, particularly as longer blades become the emerging trend. By utilizing lightweight materials, longer blades can be achieved, resulting in reduced static and dynamic loads. This not only lowers maintenance requirements but also extends the service life of the blades.
Polyurethane (PU) resins and coatings feature better performance and lower cost benefits for wind turbine blade manufacturer. With better mechanical properties as well as cost-effective manufacturing process than conventional fiberglass-reinforced epoxy blade, PU blade represents a technological leap. The combination of PU-based composite with PU infusion process allows for higher fiber matrix ratios, offering superior mechanical properties compared to conventional epoxy-based composite.
In production of very large fiber composites used in wind turbine blades, the low viscosity of PU resins results in faster infusion speed. Besides, the resins also offer the advantage of fast curing performance. Meanwhile, exceptional durability of the leading edge protection (LEP) coating based on PU provides outstanding erosion protection, reducing maintenance frequency and costs.
In a case study from Covestro and bewind, a specialist wind engineering consultancy, the use of Covestro’s PU solutions reduce manufacturing costs by up to 8% when compared to standard alternative products in a typical offshore wind farm.
Covestro’s PU resins possess low viscosity and short curing time, minimizing blade production cycles. This in turn optimizes mold occupation and reduces material and labor costs per blade. Energy consumption associated is also reduced.
Adopting recyclable materials further enhances the wind energy sector’s commitment to circular economy.
The ZEBRA (Zero wastE Blade ReseArch) consortium has recently announced the successful completion of full-scale validation testing of the first recyclable wind turbine blade and the production of a second recyclable thermoplastic blade.
The second blade, measuring 77 meters in length, is the world-first in utilizing Arkema’s recycled thermoplastic liquid resin, Elium, in manufacturing shear web, an essential structural component of the blade.
Elium-based composite components can be recycled using an advanced chemical recycling method. This involves fully depolymerizing the resin, separating the fiber from the resin, and recovering a new virgin resin and high performance glass fibers ready for reuse.
Hydrogen, which produces nearly no greenhouse gas (GHG) when burnt, is an emerging low-emission energy option for reducing carbon emissions in heavy industries and transportation, including fuel cell vehicles (FCVs) and aircrafts.
To accelerate the commercialization of hydrogen and fuel cell technology, the development of lightweight, leak-proof and safe tank systems for transportation and storage is crucial.
In the case of high-performing vehicles and aircrafts, the weight of components is of utmost importance. Plastic and fiber are the preferred choices for manufacturing tanks that are light enough for installation in vehicles and aircrafts.
Composite pressure vessels (CPVs), such as carbon fiber-reinforced plastic (CFRP) pressure vessels, are commonly used for hydrogen storage. These vessels typically consists of a thermoplastic liner with fiber wrapped around it. CPVs serve as substitutes for steel tanks while also offering corrosion resistance.
Toray, a Japanese material supplier, offers ultra-high-strength carbon fiber known as TORAYCA, which possess exceptional tensile strength. This material strengthens hydrogen tanks, enabling them to withstand the extraordinarily high burst pressure associated with compressed hydrogen.
Due to its small molecular size, hydrogen can diffuse through plastic materials. To address this challenge, Kautex has developed a hydrogen tank using special polyamide (PA) that provides high barrier properties.
The tank consists of thermoplastic liner and a fiber winding, which adds mechanical strength to ensure safety. The liner can withstand high mechanical stress and temperature ranges from -60°C to +120°C.
The plastics processing technology provider has also developed a special extrusion blow molding technology to successfully manufacture large-volume PA liners for hydrogen tank.
Notably, new bio-based materials can contribute to a higher level of sustainability for hydrogen tanks. The CUBIC project, a recent initiative in Europe, aims to develop materials with 100% recyclable intermediates derived from lignin and vegetable oils for such application.
Developing hydrogen and hydropower networks necessitates the use of reliable gas and water pipes, while plastic cable protection pipes are also essential for safeguarding electrical wires and cables. Compared to metal or concrete, plastic pipes offer greater durability and resistance to chemicals and corrosion. Also, they are lightweight and easier to install.
Steel pipes are difficult to fit in rugged terrains or environments. Plastic pipes, such as PE and HDPE pipes, are better suited for such scenarios due to their higher flexibility and reduced susceptibility to cracking. Cross-linked polyethylene (PEX) exhibits exceptional flexibility and durability, enabling it to withstand extreme pressure, making it a popular choice for pipe and tubing.
For off-grid renewable energy, lithium-ion batteries serve as primary storage where current collector film plays an indispensable role in connecting the battery to the external circuit.
While conventional current collectors typically employ aluminum and copper foil, composite current collector films with a “metal-polymer-metal” three-layer structure offer higher safety.
Due to their ultra-thin structure, these composite films increase the energy density of the battery, resulting in savings of up to 66% on copper and up to 85% on aluminum. This reduction in copper and aluminum production leads to a decrease in carbon emissions.
Biaxial stretching technology has proven to be highly effective for manufacturing composite current collector film – with both sequential and simultaneous stretching processes meeting manufacturing requirements.
The technology center of Brückner has already conducted extensive testing and identification of the best process window and film properties. As a proof of concept, several Asian film manufacturers have placed orders for the German machinery manufacturer’s film stretching lines, both sequential and simultaneous ones.
According to the International Energy Agency (IEA), as the global capacity for renewable energy continues to grow at an impressive rate, China is expected to surpass other nations in terms of capacity installations in 2024, further solidifying its position as a global leader in renewable energy deployment. Additionally, India is also projected to experience an increase in capacity additions in 2024.
On the whole, the demand for innovative plastic and processing technologies is set to rise, driven by the need to support the implementation of new energy projects.